氨作为一种兼具重要化工原料和无碳能源载体双重属性的关键化学品,不仅在工业生产中占据核心地位,还因其显著的经济附加值而备受关注。然而,传统工业技术路线合成氨需要在高温高压条件下运行,其能耗占全球电力消耗的2%,并贡献了1%~2%的人为二氧化碳排放量。在此背景下,电催化硝酸根还原反应制氨技术应运而生,为含硝酸盐废水的资源化利用开辟了新路径。该技术在温和的反应条件下即可实现高效的硝酸盐转化,在环境治理与能源转化领域展现出双重意义,为实现绿色化学和可持续能源利用提供了新的方向。
铁基催化材料因成本低廉、环境友好等优势,在电催化还原硝酸根制氨领域备受关注。然而,单一铁物种存在界面水解离动力学迟缓的缺陷,导致活性氢供给不足,进而阻碍中间产物的加氢转化,显著制约产氨选择性。更严峻的是,在大多数中性硝酸盐废水介质中,以析氢反应为代表的竞争性副反应极大地限制了制氨的法拉第效率。目前的研究多集中在金属位点的电子态调控及中间体吸附能优化策略上,而对于能够同时抑制析氢反应并增强活性的局部碱性增强机制,仍缺乏系统的探索和研究。
针对上述挑战,中国科学院金属研究所沈阳材料科学国家研究中心刘岗团队开发了一种高效的Co4Fe6合金颗粒作为电催化硝酸根还原制氨的电催化材料,其原位生成的Fead2+可自发诱导局部碱性增强,突破传统pH依赖的动力学壁垒。此外,Co-Fe双活性位点的协同作用不仅加速了界面水的解离,从而显著提升活性氢的供给效率,还增强了对NO3−的吸附能力以及后续NO2⁻的加氢转化效率,进而高效促进氨的生成。电化学性能测试表明,Co4Fe6合金在宽电位窗口与宽电解质浓度范围内均保持近100%产氨选择性,并在−0.69 V时实现98.6%的法拉第效率与97.8%的NO3−去除率,其催化活性显著优于中性介质中已报道的绝大多数钴基、铁基电催化材料。尤为引人注目的是,基于Co4Fe6合金构建的膜电极组件电解装置在工业级电流密度下,连续运行500小时后仍保持96%以上的法拉第效率,实现了氨的高效生产与固态铵盐的浓缩回收,展现出高的工程应用潜力和工业价值。
该研究成果以“Self-triggering a locally alkaline microenvironment of Co4Fe6 for highly efficient neutral ammonia electrosynthesis”为题在《Journal of the American Chemical Society》上在线发表。
原文链接
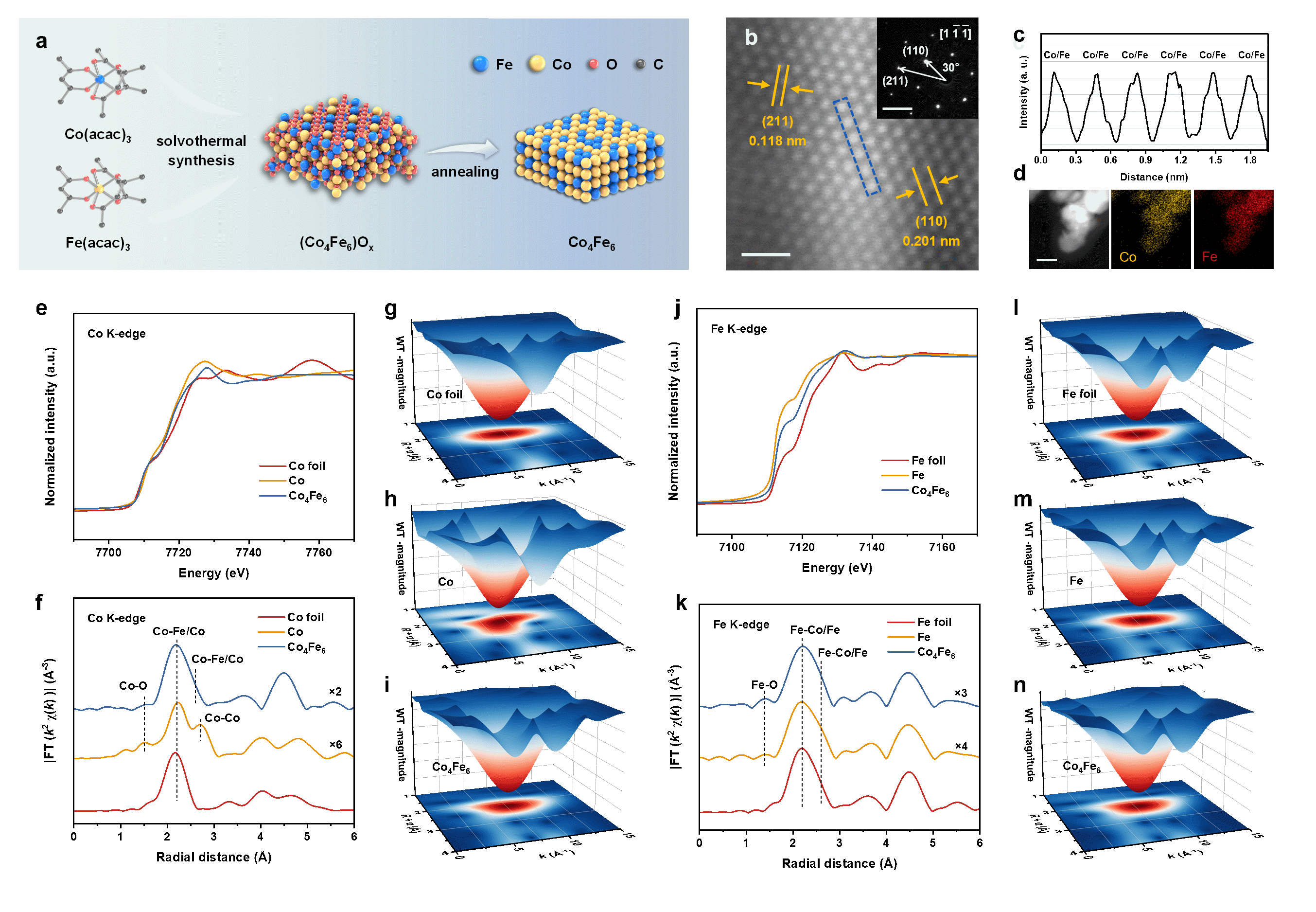
图1. Co4Fe6合金的制备方法及物相与结构表征
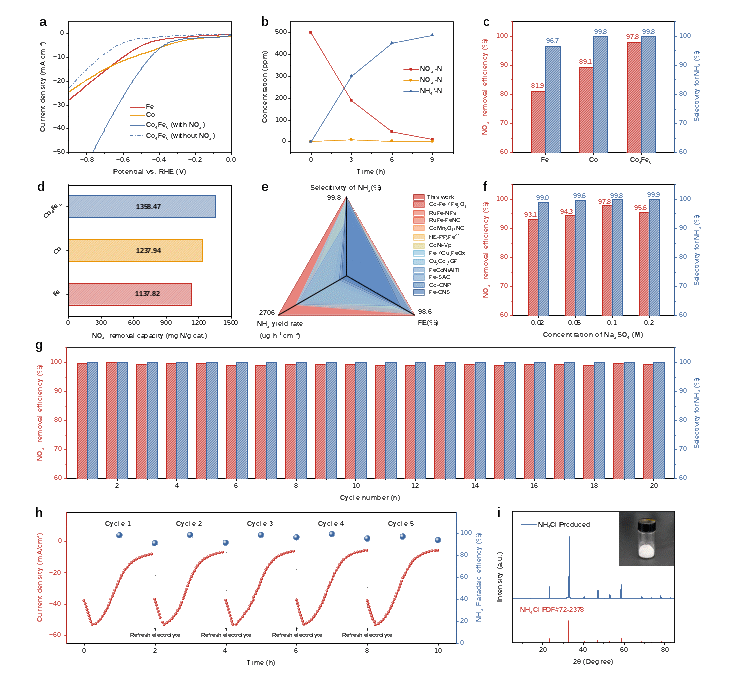
图2. Co4Fe6合金的电催化硝酸根转化制氨性能
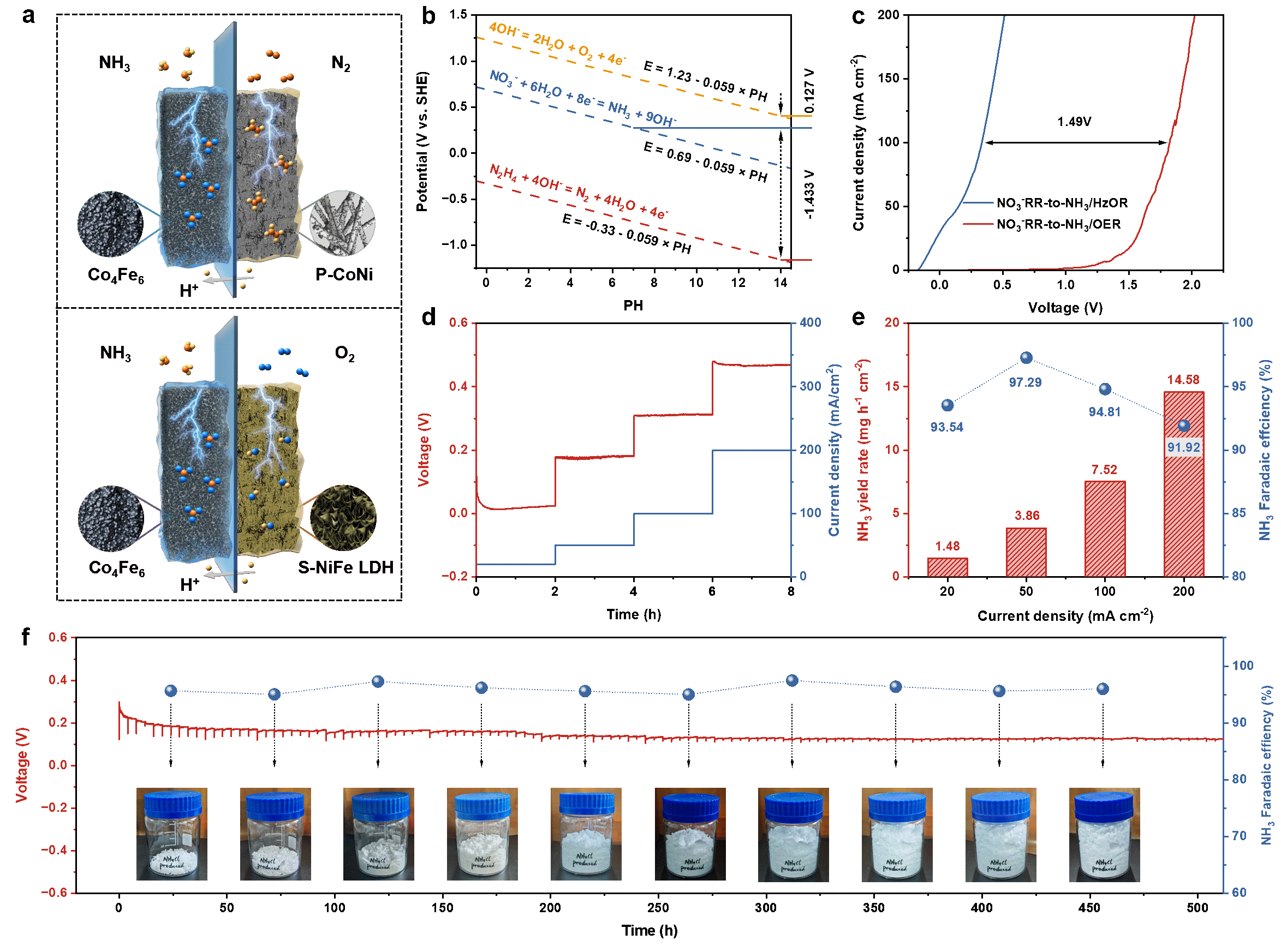
图3. Co4Fe6合金的相关器件化应用
AI科普解读:新型催化剂实现高效绿色制氨
一、氨为什么重要?
氨不仅是制造化肥的核心原料(全球80%的氨用于农业),更是未来清洁能源的潜力载体。它能像氢气一样燃烧且不含碳,还可便捷储运,被称为“无碳能源货币”。但传统合成氨工艺(哈伯法)需在500℃高温、200倍大气压下进行,消耗全球2%电力,并产生大量二氧化碳。
二、废水发电制氨
用含硝酸盐的废水直接电催化生产氨,实现“一箭三雕”:
· 环保治理:处理工业/农业废水中的硝酸盐污染(过量会导致水体富营养化)
· 能源转化:将污染物转化为高价值氨燃料
· 节能减排:反应在常温常压下进行,能耗大幅降低
三、技术突破点解析
1. 传统铁基催化剂的困境
铁虽然便宜环保,但存在两大缺陷:
· 水解离慢 → 活性氢供应不足(好比炒菜时火力不够)
· 水中易发生析氢副反应 → 大量电能被浪费(电流效率低)
2. 金属所创新解决方案:钴铁合金催化剂
金属所刘岗团队设计的Co₄Fe₆合金像精密的“纳米工厂”:
· 动态碱性环境:原位产生的吸附态铁离子自发形成局部高pH值,打破传统pH限制(相当于在反应位点自备“碱液池”)
· 双金属分工协作:
- 钴负责快速裂解水分子(每秒生产更多“氢零件”)
- 铁强力吸附硝酸根(精准捕捉原料)
- 协同加速多步脱氧加氢反应(流水线式组装成氨)
3. 性能飞跃
· 近100%选择性:在-0.69V电压下,98.6%的电能用于产氨(同类技术通常低于80%)
· 超强稳定性:工业级电流下连续工作500小时,效率仍超96%(相当于手机用两年不卡顿)
· 智能回收:通过膜技术直接生成固态铵盐,方便运输存储
四、应用前景展望
这项技术为污水处理厂和化工厂提供了全新思路:
· 分布式制氨:各地废水处理站可转型为小型氨能源站
· 闭环生产:化肥厂既能处理自身含硝酸盐废水,又能补充原料
· 海上平台应用:利用海水硝酸盐直接生产船用清洁燃料
五、小知识:为什么选择硝酸盐?
· 硝酸盐是自然界广泛存在的氮循环载体
· 工业废水、农业径流中富含硝酸盐污染物
· 1个硝酸根(NO₃⁻)可转化为1个氨分子(NH₃),原子利用率达100%
这项突破不仅让“污水变能源”成为可能,更开创了环境治理与清洁能源生产深度融合的新模式。未来或将看到更多“负碳工厂”,在治理污染的同时生产绿色燃料。