对于金属结构材料,疲劳性能是一个关键而必不可少的性能指标,是决定一种新材料能否进入实际工程应用及应用范围的重要判据。通常,材料的高周疲劳强度与其静态拉伸强度密切相关,而晶粒细化是提高材料强度的有效手段,因此以等通道转角挤压(ECAP)、高压扭转(HPT)为代表的剧烈塑性变形(SPD)工艺由于可制备块体超细晶材料而引起了广泛关注。然而,SPD超细晶材料虽然硬度和强度得到了显著提高,但塑性严重下降。在循环变形过程中,材料的微观组织结构不稳定,易发生循环软化并产生大尺度的剪切带,不仅使得其低周疲劳性能显著降低,而且造成其高周疲劳性能的提高明显低于预期以及无法进一步提高疲劳极限等问题,严重制约了此种新型结构材料的工程应用。
课题组研究人员利用搅拌摩擦加工(FSP)方式制备出块体超细晶纯铜,其组织均匀稳定,是研究超细晶材料本征疲劳变形行为的理想模型材料。研究表明,虽然FSP纯铜的拉伸强度比SPD纯铜的低,但其疲劳强度仍然得到了提高,且疲劳比提升更为明显。更为重要的是在高周疲劳变形过程中,晶粒结构稳定,没有发生异常长大和大尺寸剪切带现象,从而阐明了超细晶纯铜本征高周疲劳损伤机制为挤出。此外,与传统SPD纯铜相比,在低周疲劳变形中FSP超细晶纯铜的应变软化现象也得到一定程度的抑制,从而低周疲劳性能也得到一定程度的提高。该研究为揭示超细晶材料内在的本征变形机理提供了重要的借鉴,而且为工程领域中材料的抗疲劳损伤设计提供理论指导。
详细内容请参考文献Scripta Mater.166 (2019) 10-14;Sci China Mater. 59 (2016) 531-537;Mater. Sci. Eng. A 532 (2012) 106-110。
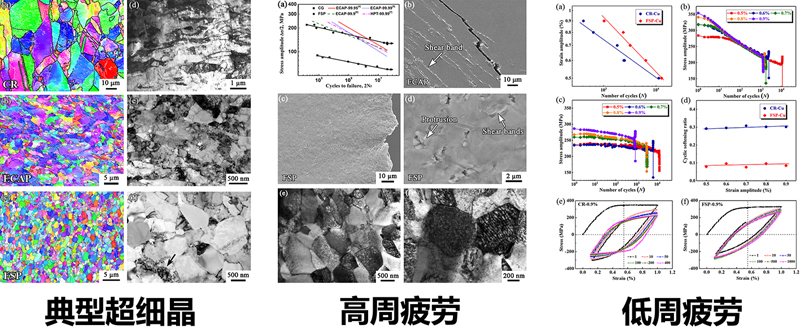