金属基复合材料MMC因为高比模量、高比强度、良好地尺寸稳定性、低膨胀系数、优良的抗疲劳等综合性能,广泛应用于航天、电子封装等领域,并向航空、车辆交通等领域扩展。复合材料坯锭的规模化制备是制约传统MMC(SiC/Al、B4C/Al等)应用的重要环节,MMC的制备过程涉及到粉末颗粒分散、合金成分优化、元素均匀化、界面反应调控、热加工组织演化、时效及析出相调控等多种关键环节。为适应相关领域对更高性能MMC需求的日益增长,亟需对以上关键环节进行更为细致、深入的组织-性能关系研究。
针对以上现状,研究团队以典型复合材料体系:SiC、B4C增强的2系、6系、7系复合材料为对象,系统研究混料、热压工艺以及热加工、热处理过程中的微观组织与性能响应规律,以期建立了一整套适合规模化制备的工艺流程。主要开展的研究内容有:(1)研究复合制备过程中的合金化过程及其对复合材料坯锭成分均匀性的影响,建立合金化和复合化一体工艺,缩短制备流程。(2)探明增强相与基体界面物理化学作用对合金元素分布、第二相种类和形貌的影响,为复合材料热处理工艺优化等力学性能调控提供了指导。(3)开展合金成分设计,增强体含量、尺寸及构型设计,研究不同合金成分及增强体等对复合材料加工及后续服役性能的影响规律,开发适合不同工程需求的高性能MMC。(4)结合数值模拟和实验手段,开展MMC塑性成型工艺-微观组织演化的研究,实现大尺寸、复杂形状MMC的高质量成型。
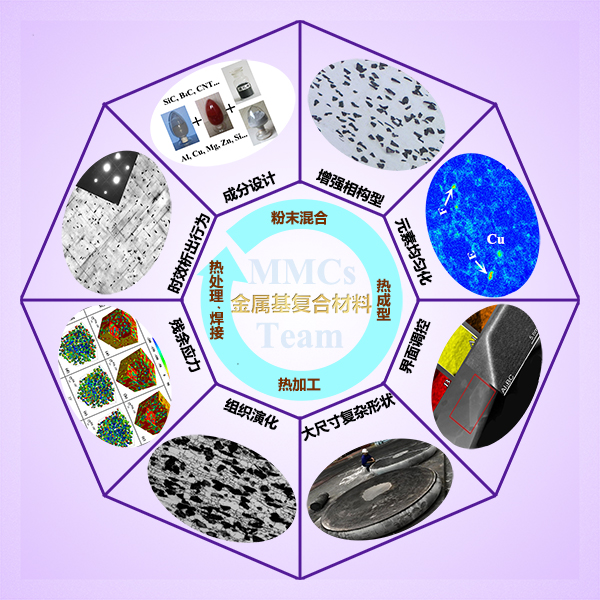