铸件是工业生产中应用最为广泛的一类构件。受工艺限制,铸造组织通常比较粗大,还伴有缩孔、缩松、夹碴等缺陷,特别是一些大尺寸、高性能要求的铸件常因为轻微的缩孔/缩松缺陷而直接报废。在不改变工件外形尺寸的条件下,实现其组织的细化、致密化、均匀化一直是行业追求的目标。课题组研究人员对铸造合金进行搅拌摩擦加工(FSP)组织重构,发现FSP能有效消除铸造组织中的孔洞、缩松等缺陷,显著细化晶粒组织,破碎粗大第二相并使其溶解到基体中,实现组织的细化、致密化、均匀化及第二相的部分/全部溶解,使材料性能显著提高。这种作用广泛适用于铝、镁、铜等铸造合金。由此建立了不改变铸件尺寸和形状、提高其性能的“FSP(+ 时效)”新工艺。
相较于铸造合金,不连续增强金属基复合材料由于含有微、纳尺度的增强相,其分散、调控难度更大。如纳米粒子在铝基体中很难均匀分散,对于纳米碳(纳米碳管,CNT;石墨烯等)增强相,还存在分散时易损伤的挑战,且损伤的纳米碳更易于与Al基体发生界面反应。这些挑战导致纳米相的增强效应难以发挥,制约了铝基纳米复合材料的发展。针对此问题,课题组人员研究了外加与原位自生两种铝基纳米复合材料在FSP组织重构中的增强相分散/形成机制。通过控制复合制备温度,抑制界面反应,进而利用FSP的均匀化、致密化功能,实现纳米碳的低损伤高效分散,进一步通过轧制或挤压实现CNT的定向分布,力学性能大大提高。同时,利用FSP加速元素扩散的作用,对未反应的Al-TiO2坯锭进行FSP,制备出均匀分散的原位Al2O3和Al3Ti纳米粒子(~80nm)混合增强超细晶铝复合材料,并阐明纳米粒子的形成机制为机械激活界面反应与溶解-析出机制。
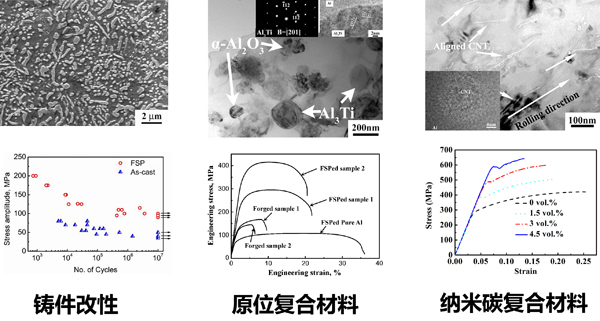